麻纺:突破技术瓶颈是重中之重
发布时间:2011-09-21 00:00 来源:TBS信息中心
开拓麻纺内需市场,除了大力发展原料行业,解决原料短缺问题外,加快科技创新,突破阻碍行业发展的技术瓶颈也是我国麻纺企业面临的一大问题。绿色纺织是未来的发展趋势,而麻类织物属环保型的功能性纤维,随着人们消费观念的转变,麻类制品将迎来广阔的大市场。
创新乃发展之源
重视技术创新并积极实施知识产权保护,如今已成为中国麻纺企业的普遍认识。湖南华升株洲雪松有限公司以提高企业技术创新能力,搞好知识产权保护,特别是进一步做好海外知识产权保护工作这一工作思路作为企业发展、做大做强的立足点,鼓励科技人员积极开发新产品,大力提升了产品附加值及品牌价值。
体验到保护好知识产权对公司发展巨大的推动作用后,株洲雪松先后有13项发明申请了专利,其中3项发明已分别在美国、欧盟、日本获得授权,6项发明已在国内授权,其余4项分别已被中国国家专利局,美国、日本等国家的国家专利局正式受理。2010年,株洲雪松获中央财政部设立的PCT申请专利资助资金65万元,成为全国获得国际专利申请资助最多的企业。
四川玉竹麻业通过持续的技术创新,已完成国家专利申请4项,协助并参与制定行业技术标准1项,自主研发新产品多项。
根据市场需求,玉竹麻业从原料选择、脱胶工艺应用、高档麻条生产、梳理和混纺工艺确定、混纺原料比例确定、主要设备选型等方面入手,通过逐一的技术攻关,成功地开发出72公支纯麻纱、50公支麻粘纱、58公支麻维纱,可达到100公支高档纯麻布面料标准。此外,通过多年的艰苦摸索,玉竹成功地开发出具有自己特色的“绢纺+毛纺”式组合梳理工艺。目前,玉竹麻业生产的04、05号麻条,已较好地克服了苎麻织物的刺痒感。
近年,麻纺行业技术改造步伐不断加快,先进技术装备的投资不断增加。通过国内装备制造技术的升级和引进国外先进技术设备,行业整体装备和技术水平大幅提高。目前亚麻纺织与国际先进水平设备的比重已达到60%以上;麻纺无结头纱率已达到70%、麻纺织无梭化率60%以上。麻纺技术装备水平的整体提升,为全行业的经济运行和效益提供了良好的市场机遇与发展平台。
环保是必然趋势
精细化麻类纤维加工、湿纺亚麻粗支纱项目、大麻脱胶、300公支纯苎麻织物等一系列自主创新的新工艺、新产品、新技术的推广和应用,有效地提高了麻纺织产品的附加值,扩大了出口,增强了国际市场的竞争力,为促进麻纺产业升级产生了积极的促进作用。
新申集团把节能减排工作作为企业义不容辞的社会责任和持续发展的重要举措,成立了节能减排工作领导小组,明确了新申集团节能减排目标,制订了各项能耗、物耗、环保和成本指标,完善了节能减排考核办法,将节能减排指标层层分解到各分厂、车间、班组,各项指标完成情况与奖金挂钩,大大激发了职工立足岗位、节能减排的自觉性和积极性。通过技术改造,采用节能环保新设备、新工艺、新技术,新申集团近年来大力实施科技创新,以新工艺、新技术的运用引领节能减排工作向纵深推进。在亚麻纱、亚麻面料生产方面,新申集团投资200多万元实施了亚麻技术改造,大幅度降低了生产成本,仅电耗一项每年就创经济效益60多万元。
常州美源亚麻纺织有限公司采用了氧漂及酶处理技术,替代传统“亚氧漂”工艺,解决了目前大多数企业用含氯漂白制剂脱胶、漂白亚麻粗纱污染环境的问题,缩短了工艺流程,降低了能源消耗,据估算,可节电45万度,节约蒸汽1750吨,节水4.5万吨,折合成标煤288.3吨,排污达到国家三级排放标准,进入城市管网。
重庆涪陵金帝工业集团有限公司采用自主研制的JD-1型苎麻脱胶助剂进行快速煮练,达到快速脱胶的目的;采用自主研制的JD-1型牵伸机替代拷麻机,达到减轻工人劳动强度,脱胶均匀的目的;采用自主研制的新型漂酸洗油联合机工艺代替老漂酸洗、给油工艺,每年可节约用水72万吨,节约用电36万度,节约蒸汽33000吨,折合少用标准煤4650吨。
技术瓶颈待突破
《纺织工业“十二五”科技进步纲要》明确提出,“十二五”期间,麻纺行业要重点突破的技术是“先进高效、低耗、环保的麻类纤维纺纱专用技术及装备”,其中主要是苎麻带状精干麻、牵切纺工艺技术装备的研制。
中国麻纺行业协会副会长、秘书长董春兴对此解释说,由于麻纺织行业规模小,长期以来限制了设备的创新发展。特别是苎麻设备长期处于落后状态,没有大的纺机企业专注开发,基本是麻纺企业在棉纺、毛纺、绢纺设备上进行零敲碎打的改造,长期缺乏定型设备。董春兴希望国内有实力的纺机企业能加大对苎麻成套设备开发和改造的关注。据了解,目前,郑州纺织机械股份有限公司正力求在苎麻设备上有所突破。
麻纤维长度较长,为了便于与棉等纤维混纺,需要牵切纺把麻纤维切断成一定长度,这样可以利用棉纺定型设备进行生产。董春兴介绍说,东华大学的专家已经与企业一起进行过相应研究,但目前还没有定型产品,期望“十二五”期间能完成技术优化和工艺设备定型,并在行业内推广。
脱胶产生的污染一直是制约行业发展的大问题,企业大多采用化学脱胶的方法,尤其是苎麻脱胶基本是采用人工。董春兴说,目前采用生物或生物酶技术进行脱胶在部分企业已开始应用,有的效果不错,有的效果一般,基本上还在小试或中试阶段,生产稳定性还有待提高,没有大规模推广应用。
麻纺行业是典型的劳动密集型行业,万锭用工在300~500人,大大高于纺织其他行业用工人数,这在招工难日益突出的今天,成为行业要解决的突出矛盾。而苎麻减量脱胶、快速脱胶技术正是为了减少用工,减轻工人劳动强度。此外,由于流程缩短,还节约了水电,提高了效率,减少了污染的排放。
董春兴认为,只要脱胶技术过关了,成熟了,设备能做到减少用工,减少污染排放,企业就会积极地去应用。他希望“十二五”期间,万锭用工能在原来的基础上减少100~200人。
订阅轻纺原料网
每天了解宏观经济政策、国内外形势、原料价格行情
微信号:tbs2007
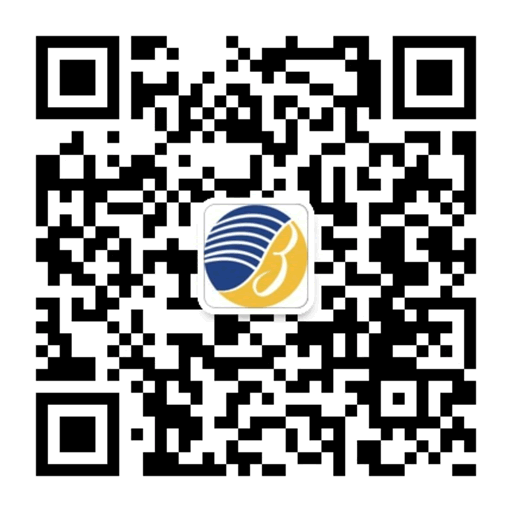